Maintenance fundamentals
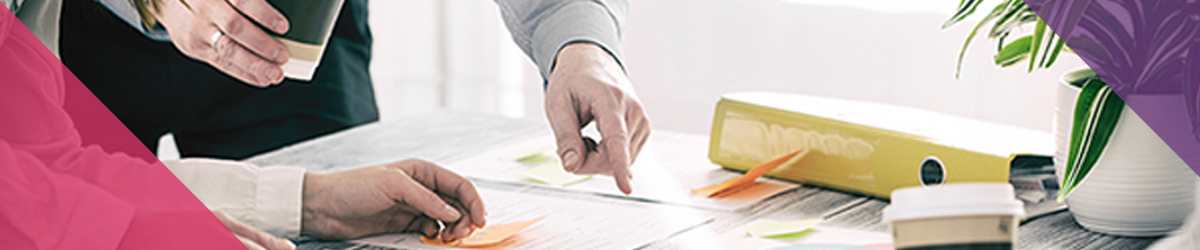
Course Summary
In the first of a series of two courses aimed at upskilling your maintenance team to bring about huge business benefits, including reduced maintenance and production costs and increased safety and profits, the NMIS Manufacturing Skills Academy and Project Engineering Management Ltd are delivering a specialised in-person two-day course covering the fundamentals of creating a robust maintenance strategy.
This course features best practice maintenance techniques, including task selection, failure analysis and continuous improvement, and is perfect for people relatively new to the industry and more experienced plant professionals looking to improve plant performance with a clear step by step strategy.
It will inspire your maintenance team to lead, develop and sustain world-class performance whatever your sector, touching on technologies and opportunities within the world of industry 4.0 and can be taken as a stand-alone course, or followed up with, ‘How to use Reliability Centred Maintenance (RCM) to optimise maintenance.'
Where:
The course will take place within the new NMIS flagship facility next to Glasgow Airport, which includes a fully connected Digital Factory, the NMIS Manufacturing Skills Academy and a publicly accessible collaboration hub. All delegates will receive a tour of the new facility.
Testimonial:
“Highly beneficial training for professionals in engineering project management, quality management, operations, as well as supply chain personnel from manufacturing organisations.” August 2022
This course has limited spaces available. Should you be unable to attend, please cancel your booking to allow us to re-allocate your place.
Failure to cancel and or attend may result in you being removed from any future courses.
The following topics will be covered in this course:
- Understanding and measuring reliability- measures and steps required to address reliability issues
- Maintenance strategies- traditional approaches, tools and techniques including reactive, preventive and predictive maintenance; the use of data and technology in industry 4.0
- Failure analysis and continuous improvement- establishing asset importance, priorities and risk; failure analysis and root cause analysis (RCA); continuous improvement of maintenance plans and performance
- Developing, implementing and managing maintenance- planning and scheduling with the effective use of resources; managing spares; building a strong culture with skills development and management of change
- The future of maintenance optimisation- new developments in technology; a roadmap for the future
The learning outcomes for the course are as follows:
- Recognise reliability definitions and measures used to address maintenance issues
- Select the most suitable maintenance approaches and technique
- Utilise processes and technologies to gather data, analyse and optimise your industry 4.0 maintenance strategy
- Incorporate risk management and root cause analysis (RCA)
- Plan for the future and continuously improve asset performance
The course is suited to engineering, asset management, maintenance and reliability personnel working within or supporting manufacturing, industrial, oil and gas and energy sectors with responsibility for the application and improvement of maintenance plans, processes and procedures.
This course is being delivered by Project Engineering Management Ltd.
Established in 2015, Project Engineering Management Ltd is a specialist engineering consultancy providing maintenance training, asset management and project management solutions.
Matthew Laskaj is a Chartered Mechanical Engineer, Fellow and Chair of the Institution of Mechanical Engineers Scottish Region. As a specialist engineering and maintenance trainer, he has worked with companies in a variety of industries worldwide. Originally from Australia, Matthew started his career working in a food manufacturing plant where he was responsible for setting up a new reliability program. The next 5 years were spent as a mechanical and reliability engineer within steel works and refineries across Australia.
Matthew now lives in Scotland where he is director of a project management and engineering business he set up having worked throughout Scotland in manufacturing plants and refineries before settling in Aberdeen in the Oil and Gas Industry as Engineering Manager of a drilling company.
Over the last 8 years working as a trainer, and continuing his involvement in the management of projects, Matthew has enjoyed the variety of work the role brings. But he says the real reason for choosing to do what he does is the people he gets to meet and continue to help along the way.
Booking fee: £1000 per delegate
Dates & Venues
Date | Register your interest |
---|---|
Location | NMIS Netherton |
Duration | 09.00 - 16.30 each day |
Cost | 1000 |
In collaboration with
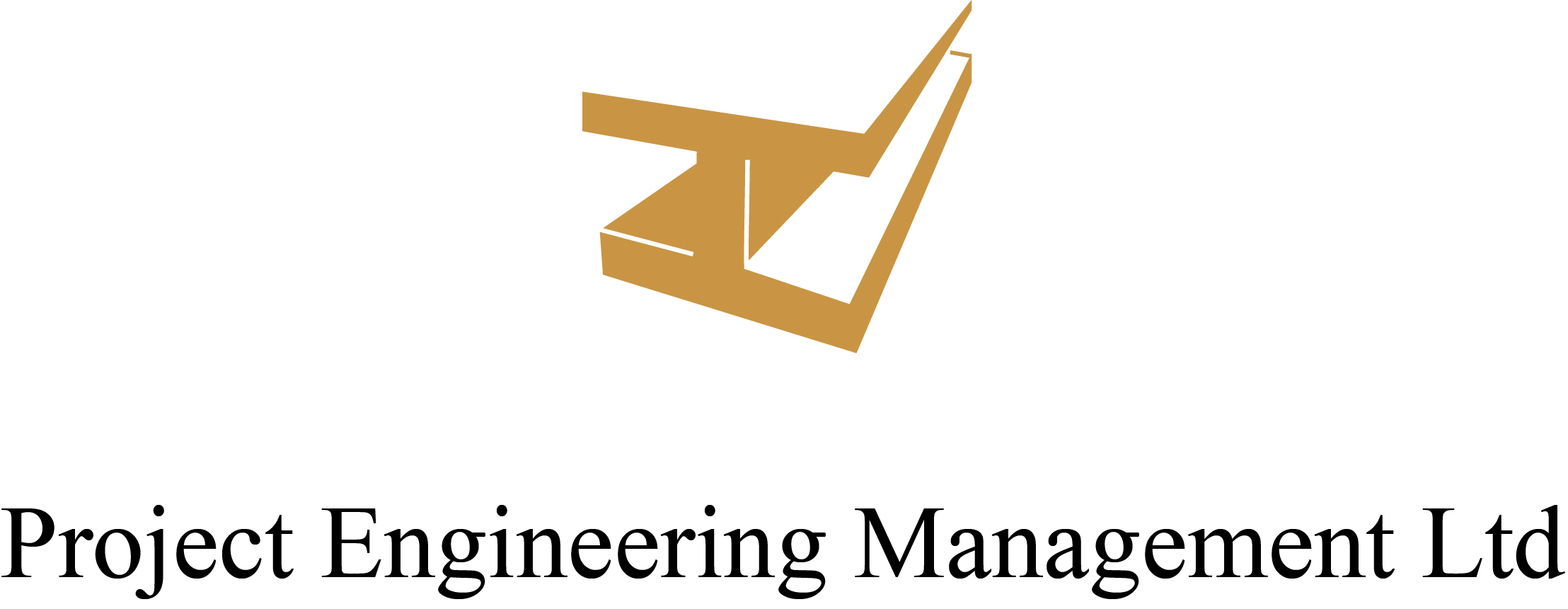