Tinsley Bridge Group
Tinsley Bridge Group
Family-owned Tinsley Bridge Group is based in Sheffield and manufactures components for the automotive, nuclear, rail, defence, renewables and energy sectors. Offering 175 years of materials experience, it uses upset and open die forging among its various manufacturing processes.
Challenge
Tinsley Bridge was exploring automating its forging processes with the aim of boosting productivity. It was keen to examine current forging operations and implement any necessary changes before investing in new automation technology.
As a busy gro
wing business, they required a fresh perspective, one with relevant forging expertise, that could help them take a step back from the day-to-day business. This would help identify key areas for improvement before taking the next steps towards automation.
How did the AFRC help?
The AFRC specialises in forming and forging research and the engineers, researchers and business professionals within its forming and incremental technologies (FiT) team bring significant forging research expertise and industry experience.
Two members of the team, including the AFRC’s chief of forging, visited the plant where they conducted an automation review, funded by Innovate UK. They took part in a walk around and focused on the forging line used to make safety products for heavy vehicles, which Tinsley Bridge had identified as a potential area for improvement.
Here, steel bars are induction heated, upset, and then forged at each end to create key product features. Operations on various presses within forging cells, along with a bending operation and associated heat treatments, were all under review.
The AFRC’s forging specialists created a comprehensive report which included photographs, useful contacts and key recommendations that Tinsley Bridge could implement to tighten up its processes and boost efficiency, before continuing with its journey towards automation.
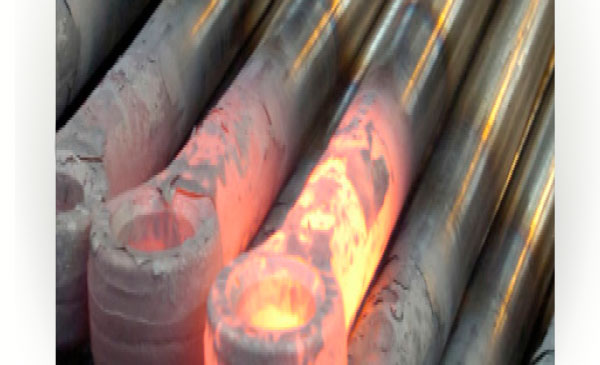
“Working with the AFRC went way beyond our expectations. It helped us identify a number of areas that we can work on to prepare for automation, at the same time boosting our efficiency and productivity more generally. The quality of forged parts we are producing since implementing these recommendations is now at the highest level that I have seen during my time here.
“This project allowed us to take a vital step back from day to day operations and look at the bigger picture. The process took us back to basics, enhancing our skill levels and allowing us to adopt a lot of the recommendations within the report.
“We really appreciate the AFRC’s expertise and enjoyed building up an excellent working relationship with the team. We certainly hope to collaborate again in the future.”
Russell Crow, Director of Engineering and Development, the Tinsley Bridge Group
Business impact
It is essential that procedures and processes are repeatable and accurate before a business embarks on automation.
Recommendations included clamping improvements within the tooling that hold parts in place during forging to improve the capability of the forging process. The introduction of lubrication was also suggested to help extend tool life and reduce die wear, while making it easier to release components from tools. This would speed up the overall forging process and make it more efficient.
Switching from gas burners to infrared die heating would be more efficient than using an open flame due to increased time to reach target temperatures, which would improve part quality and die life.
A number of the AFRC’s recommendations have now been implemented, helping Tinsley Bridge better prepare for automation while also significantly boosting its productivity, cutting costs and improving part quality.
As a result of these recommendations, in particular the uses of lubricants, it is estimated that tool life has improved by more than 10%.