TGM Lightweight Solutions
TGM Lightweight Solutions
The National Manufacturing Institute Scotland (NMIS) collaborated with German lightweighting specialists TGM Lightweight Solutions to design a car battery concept that can reduce weight, production costs and vehicle CO2 emissions, while providing an improved battery life expectancy, without compromising on power
What challenge did TGM face?
Automotive manufacturers must meet customer demands for increased space, power, and features within their vehicles while contending with tightening CO2 regulations and remaining competitive. As we move towards net-zero global emissions by 2050 and see an increased appetite for electric vehicles, the need for efficient low-cost batteries has never been greater.
How did NMIS help?
TGM Lightweight Solutions devised a patented design for a starter battery using a LiFePO4 battery cell. They collaborated with the NMIS Design Engineering team across all stages of concept creation including design analysis, weight reduction optimisation, method of manufacturing assessment, and overall cost estimation, focusing on a starter battery for a BMW F15, which is a popular mid-size luxury SUV. The team identified that a technology change from lead to lithium iron phosphate would create a lighter and smaller battery, and devised an improved lightweight design for the modular battery case focusing on reduced weight and manufacturing costs. Combining expertise and embedding NMIS manufacturing knowledge early into the design process ensured the rapid development of a proven concept that is highly cost-effective, sustainable, and ready for transformation into an industry demonstrator.
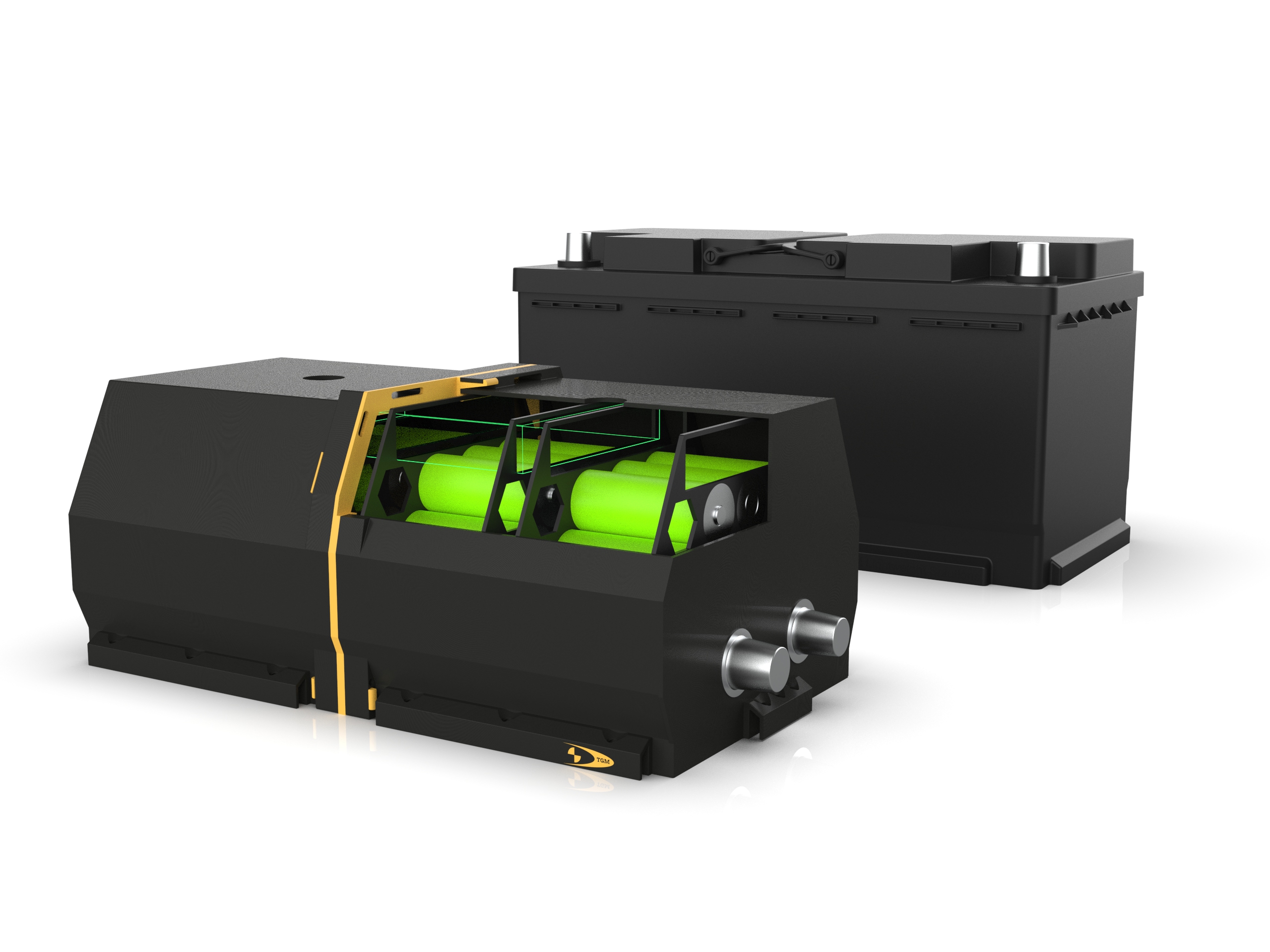
It’s great to see the puzzle come together. By collaborating with NMIS, we could successfully estimate the weight and cost of a product right from the start. I’m excited to see the positive impact.
Florian Wätzold, Consultant / project manager, TGM Lightweight Solutions GmbH
We’re eager to see the positive outcomes of this new battery concept on industry and explore further avenues.
Ralf Utescheny, Head of Innovation and NetworkCoordination, Koller Kunststofftechnik GmbH
Most new vehicles still use a highly inefficient starter battery technology based on lead – acid. In terms of efficiency, power-to-weight ratio and space requirement, this has barely been improved over the last century.
Frederic Dietze Founder and CEO, LITEWERKS engineering
Business impact
This starter battery concept could radically reduce the weight of batteries in electric and internal combustion engine vehicles. Weighing just over 7kg, it offers a 33kg saving compared to the two standard lead-acid batteries currently required for a BMW F15.. Providing a Co2 emissions reduction of around 4g/km, the smaller battery system also offers manufacturers options for enhanced comfort within sports cars and electric vehicles and production cost savings of between £10/kg to £15/kg depending on volume. The new chemical composition also offers extended battery life and opportunities for recycling.