Safran Landing Systems
Customer challenge
Safran Landing Systems is a world leader in landing and braking systems for both civil and military aircraft and helicopters, including landing gear, wheels and brakes and other associated systems.
The company wished to address the issues of cost, wasteful material and the long lead-times involved in the manufacture of a commercial aircraft landing system component.
Safran approached the AFRC in order to investigate alternative methods of manufacturing this component that would be more economical.
How did NMIS help?
Researchers and engineers from the AFRC’s forging and incremental technologies team carried out a series of trials on the component using the WF STR600 flow former machine. Various types of materials were tested in conjunction with carefully selected heat treatments as advised by the AFRC’s materials science team.
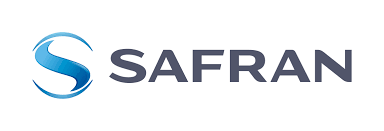
Jean-Philippe Villain-Chastre, Research and Technology Programme Manager, Safran Landing Systems stated:
Working with the AFRC went way beyond our initial expectations. Not only did we appreciate the AFRC’s expertise but we built up an excellent working relationship and we hope that there will be an opportunity to collaborate again in the future. We now plan to build on this success, streamline the manufacturing process of our other landing products so that Safran can continue to deploy the most advanced engineering in this field.
Business impact
The trials were so successful that the results exceeded the client’s expectations. The AFRC’s in depth knowledge of metals and materials science established that if this alternative manufacturing method is implemented, costs could be cut by at least 50% due to a reduction in material wastage. Flow forming is more environmentally friendly than traditional manufacturing techniques as less raw material is required. These savings would allow Safran to increase its capacity to assist with supply and demand in the commercial airline market.