WEIR Group
Mining company digs into alternative manufacturing routes to validate its existing approach
Background
The University of Strathclyde's Advanced Forming Research Centre (AFRC) worked with mining equipment company the Weir Group to explore switching from casting to forging for the production of its bucket teeth to validate its current approach or potentially adopt a new method.
The AFRC has made recent advances in forging, integrating data to offer potential time and cost savings and superior performance.
Customer challenge
Bucket teeth are attached to an excavator to penetrate the ground. The Weir Group currently manufactures its broad product range through casting. The company sought to determine whether forging would provide similar or higher levels of durability while reducing material waste, or confirm if casting is the best option.
How did the AFRC help?
The AFRC selected three Weir Group products that were produced through casting as part of the feasibility study. An alternative forging route for each was then proposed, analysed and improved using a finite element (FE) method.
As part of the project, a cost calculator was also provided, providing the Weir Group with all the data required to make an informed decision on whether forging would deliver its desired outcomes.
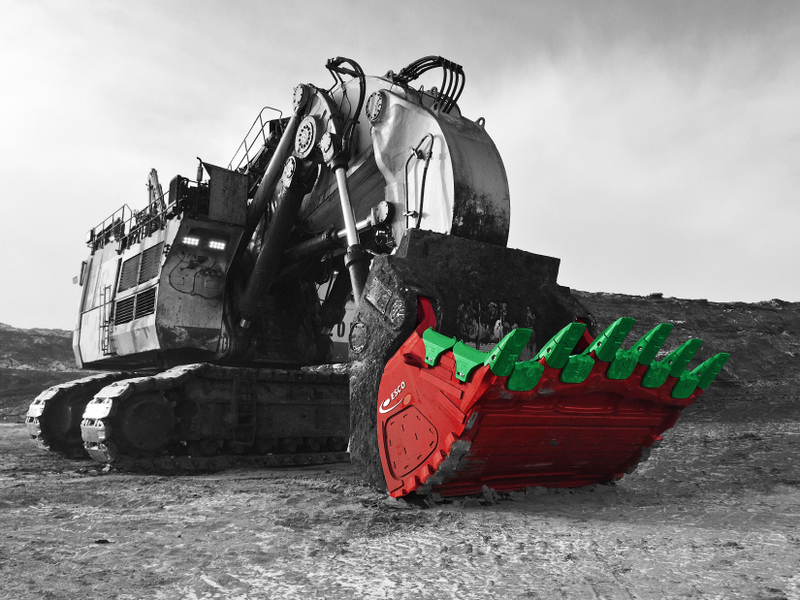
Lauren Youd, Senior Project Manager, the Weir Group, said:
Through the work with the Advanced Forming Research Centre, the Weir Group was able to explore the potential of forging as a viable option.
“The outcome of the project was positive, as forging was able to be discounted due to the nature of certain product geometries, ensuring current production methods present both the most cost-efficient and high-performance outcomes available.
Business impact
This project demonstrated to the Weir Group what forging can offer, producing various different durable products quickly with limited waste.
As a result of the work, the Weir Group was able to determine the business outcomes of embracing this manufacturing route and, after careful consideration, rule out forging as a more suitable method for producing its specific products.