3D printing technology delivers sustainability at sea
3D printing technology delivers sustainability at sea
Background
Marine Vessel Lightweighting (MariLight) is a collaborative R&D project funded by the Clean Maritime Demonstration Competition. It aims to provide the maritime sector with a pathway to adopting large scale additive manufacturing (LSAM) of lighter, topology optimised shipbuilding components, moving from traditional, manual fabrication processes to an automated, flexible, and more sustainable rapid manufacturing route.
The first phase of the project was led by Malin Marine Consultants and supported by the National Manufacturing Institute Scotland (NMIS), Altair Engineering, BAE Systems, and Lloyd’s Register.
Challenge
The maritime sector is vital for the global economy, facilitating the transportation of the vast majority of internationally traded goods. However, the movement of products comes at an environmental cost, with merchant ships burning around 300 million metric tons of fossil fuels each year and emitting approximately one billion metric tons of CO2[1].
By 2040, the International Maritime Organisation is aiming to reduce the volume of CO2 from shipping by at least 70%[2]. The MariLight feasibility study seeks to address this challenge by implementing lightweighting measures in ship structures, thereby lowering the volume of steel used in shipbuilding and reducing the total power required to propel a vessel.
What did NMIS do?
NMIS’ role in the project was to deploy topology optimisation (produced by Altair Engineering), along with LSAM, to deliver lighter and more sustainable components for marine vessels. The team identified three parts of the ship for potential weight-saving:
- Bilge pump foundation
- Windlass foundation
- Bulbous bow
Of the selected components, the bilge pump foundation and bulbous bow are found on the underside of the vessel, a confined area that is typically difficult for welders to work on, and poses a potential health and safety risk. In accordance with industry requirements, they were designed with optimum stiffness-to-weight ratio and minimum material usage. NMIS helped to manufacture and test a demonstrator section of the topology optimised bilge pump foundation; all witnessed by Lloyd’s Register and backed by their standards.
The team adopted wire-arc additive manufacturing – a method of direct energy deposition for metal 3D printing – to develop an automated process for manufacturing the components. A computational model was also developed and validated to predict thermal and distortion behaviour, serving as a valuable tool for subsequent project phases.
[1]The shipping industry faces a climate crisis reckoning – will it decarbonise?
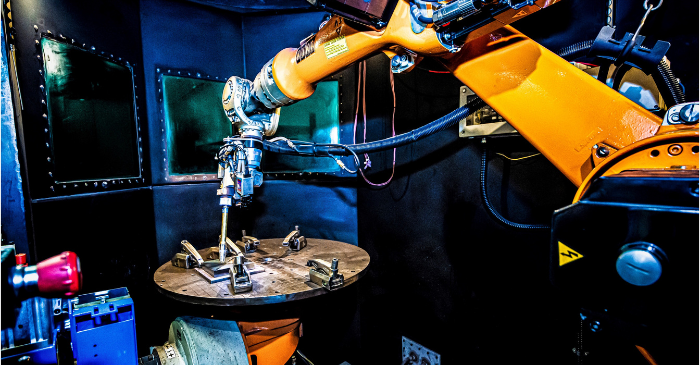
Chris Dunn, managing director at Malin Marine Consultants, said:
We’re really pleased with the progress we’re making so far and it’s great to see the maritime sector embracing greener manufacturing methods. Now that we’ve successfully trialled the performance of LSAM, the next step will be to test its functionality in an industry-like environment. It’s been a privilege to collaborate with the team at NMIS and we look forward to building on this partnership in the future.”
Business Impact
With traditional shipbuilders sometimes hesitant to adopt modern technologies, the project is helping to raise the profile of the reliability of LSAM for manufacturing components.
From the topology optimisation, results of the new designs show between 24% to 53% weight reduction, as well as other enhancements including structural strength. Meanwhile the overall weight of the ship could be cut by approximately 16%, with potential to save an estimated 7.7 million tonnes of steel across the global fleet.
By using LSAM methods, the raw materials would be more readily available, opening opportunities to reshore supply chains and reduce lead times for parts. The streamlined manufacturing could lower CO2 emissions by 37% and the use of materials by 35%.
The next phase of MariLight will involve printing pre-deployment demonstrators, while producing a business case to document activities, further lifecycle assessment and cost modelling, and overall conclusions of the project.